Katelyn Geleynse presses the button and the machine groans to life. The massive metal plates shift until a half-ton of compressed plastic tumbles out onto the waiting pallet. The crowd cheers. Permanent markers are passed around and everyone takes turns signing the massive block.
It’s February 16, 2024, and the members of the Promega Sustainability Committee are gathered to witness the first bale of plastic film being ejected from the Madison campus’s new baler. It’s only the first bale, but it represents a major step in the company’s efforts to reduce plastic waste.
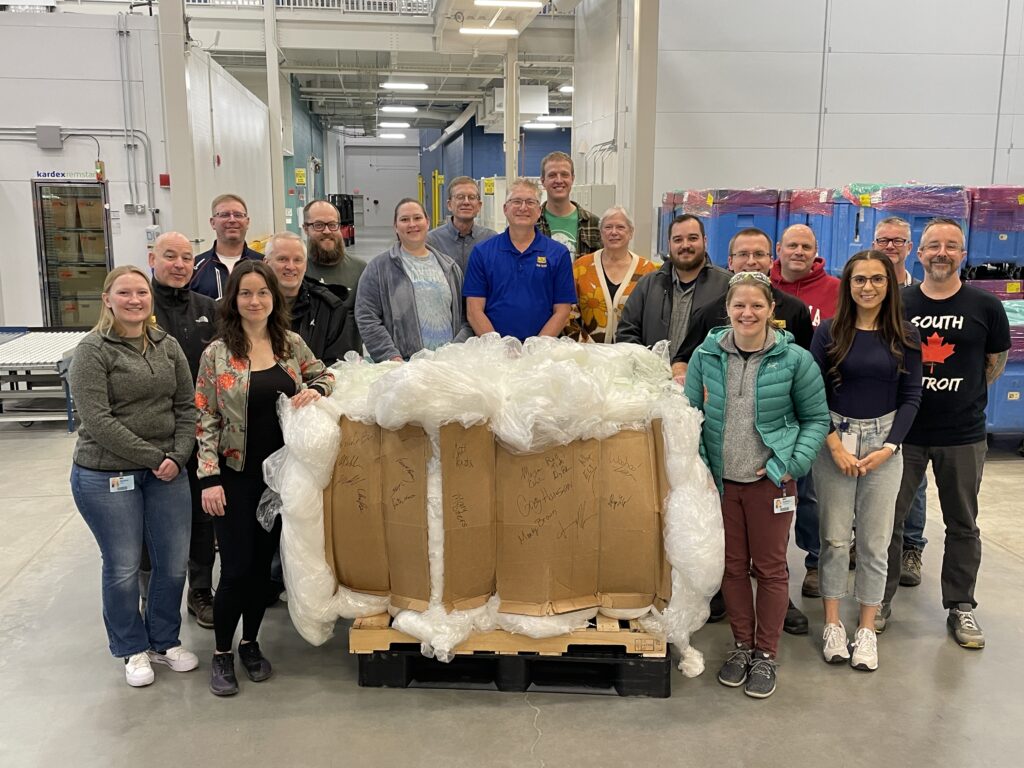
“All of this would have gone to the landfill if we hadn’t set up this program,” Katelyn says. “It feels good to know that at least some of my waste is getting a second life.”
Plastic film is notoriously difficult to recycle and takes decades to break down in a landfill. The Promega initiative to divert this waste was started by a small group of employees who noticed a problem and worked for over a year to build a sustainable solution. What began as a small volunteer operation grew to spur capital investment in a process that will rescue around 35,000 pounds of plastic per year.
Ideas into Action
Katelyn Geleynse isn’t a full-time recycler for Promega. As a Production Scientist, she contributes to the bulk manufacture of certain regulated Promega products. However, she has a passion for reducing her environmental impact that influences how she thinks about her work.
The Promega Sustainability Committee is full of passionate employees like Katelyn. This group volunteers their time to promote sustainability initiatives in the company. Often, this is through educational opportunities and hands-on events like electronics recycling or electric vehicle test driving. Other times, they identify a problem at work and brainstorm and collaborate to find a solution.
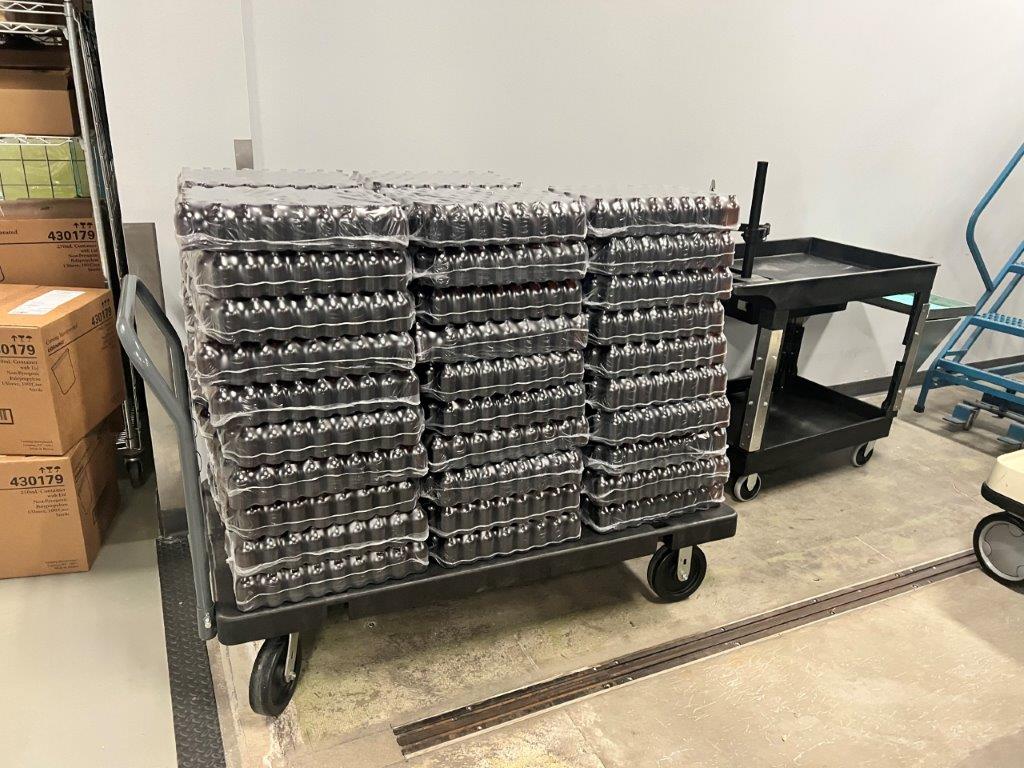
In 2022, several members of the committee noticed that a large volume of plastic film produced by Promega labs and operations processes was not being recycled. Promega has long worked to reduce our plastic waste – we’ve adapted many kit packages to eschew shrink-wrap, enlisted in a glove recycling program, and worked with suppliers to reduce the packaging coming into our facilities. However, we were still throwing out non-recyclable plastic films.
“We’re talking about any plastic material you can stretch,” says Greg Hansen, Environmental, Health & Safety Supervisor. “You can poke your finger through it. When you crumple it up, it doesn’t make a lot of noise.”
Some of this material comes from research labs – wrapped around a new pipette tip box, for example. The majority comes from manufacturing facilities. Promega complies with myriad regulations and quality standards, so as a result, much of the material coming into manufacturing is double-bagged for sterile transport. The Sustainability Committee decided to explore strategies to divert this waste from the landfill.
They first went to the company’s current recycling service provider. That provider was unable to accept the films because there was too much contamination in the form of labels, ink and dye. The team next reached out to NexTrex, the community recycling program run by composite decking company Trex. They shared samples of the most common types of film discarded at Promega. NexTrex said the materials met their criteria, but they could only pick up film in bulk – ideally, a full trailer at a time.
At the time, the team had no way to compress and store the quantity of film they would need to fill a trailer. They had to start by finding a smaller win.
Applications Scientist Melanie Preston contacted someone she knew at a local grocery store chain. Their stores already partnered with NexTrex to recycle massive volumes of film each month. They had their own baler to compress plastic films into dense blocks to transport for recycling. As the bales filled a trailer, they would be collected by NexTrex. The store agreed that if Promega could deliver the film they collected to the baling location, it could be mixed in with store’s regular loads to be compressed and collected.
“We set up a collection container at our Feynman Manufacturing facility, because that was the largest producer of the film at the time,” Greg says. “That was so well received that we expanded to three other buildings. Soon we had appointed Building Champions across campus to monitor the bins and work with Distribution Services to manage collection. Everyone who caught wind of our efforts wanted to get on board.”
Focus on Sustainable Growth
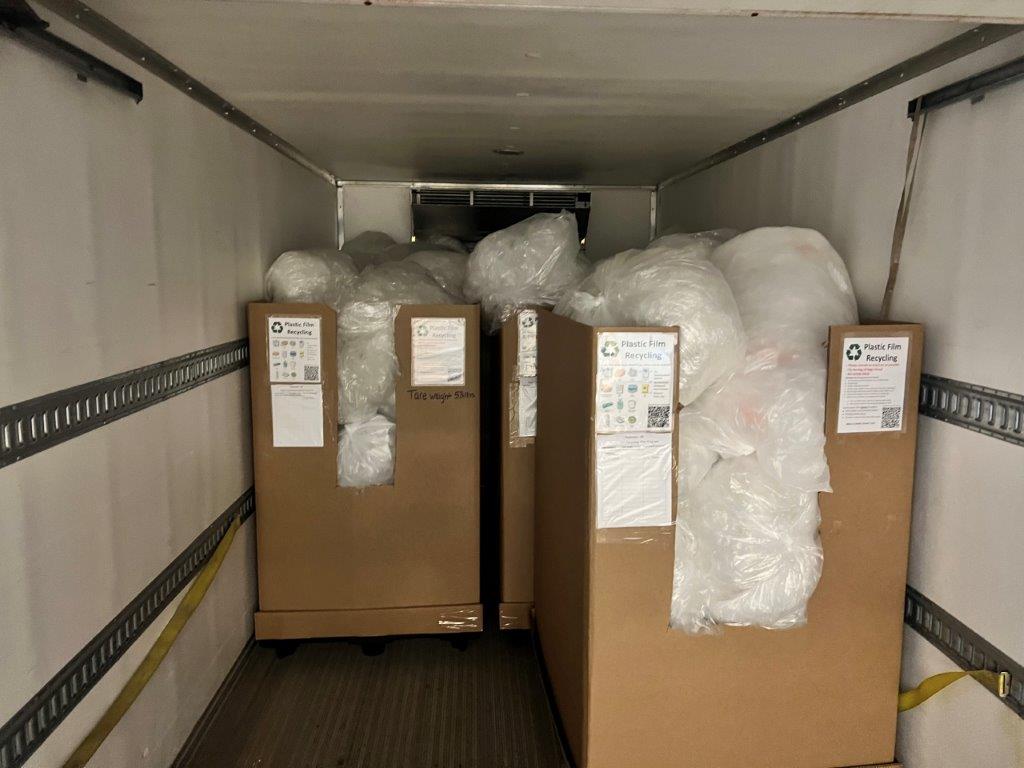
In the first four months of the pilot project, Promega delivered over 7,000 pounds of plastic to the grocery store. The project was considered a smashing success except for one small problem – the deliveries from Promega had grown so much that the grocery store could no longer handle the extra.
“We ended up overwhelming the capacity at the grocery store,” Melanie says, smiling. “By early 2023, we were going to the grocery store twice a week. We knew our pilot project was clearly a success, but for it to continue we had to find a way to bring the processing in-house.”
The team met with NexTrex to understand their requirements and recommendations. They identified a baler that would allow Promega to prepare their own plastic film bales for pickup by NexTrex. However, they couldn’t just buy the enormous machine and shove it in an empty corner somewhere. They had a lot of details to figure out, and they needed Promega leadership to approve the program.
“There was never any resistance,” says Zack Wermeling, Production Scientist. “Everyone, especially leadership, understood how we were supporting our corporate sustainability goals. But we couldn’t just go for it – we needed a firm plan that addressed logistical concerns and justified the investment of money and human resources.”
Eric Teigen, a Project Coordinator in Distribution Services, provided critical guidance to the team as they selected a location, prepped for installation, and wrote the official capital expense justification.
“It’s an expensive piece of equipment, so you have to answer a lot of questions,” Eric says. “Why do we need it? What benefits will it have? What other departments will it affect?”
Kepler Center, the main logistics hub supporting the global Promega supply chain, was recently renovated and expanded – nearly doubling in size. One of the loading dock areas originally used for outbound shipping was slated to have minimal traffic after the new construction opened, so Logistics Manager Chad Graffin suggested it was the perfect spot to install the baler. The expansion also created enough space to store the bales on warehouse racks until there were enough to schedule a pickup.
“It’s perfect – it’s almost like that area was designed for it,” Chad says. “It was originally used for domestic and international shipping, but now the baler sits there perfectly.”
Along with the logistical concerns, the team also had to build a process to efficiently collect film from every building, transport it to Kepler, compress it and load it into the trailer. Distribution Services took on the bulk of this work, with the support of the Building Champions around campus.
“We didn’t want to come in as outsiders and assign people work they didn’t sign up for,” Zack says. “After some back-and-forth, we came up with a great plan backed by everyone who’s involved.”
Moving Forward
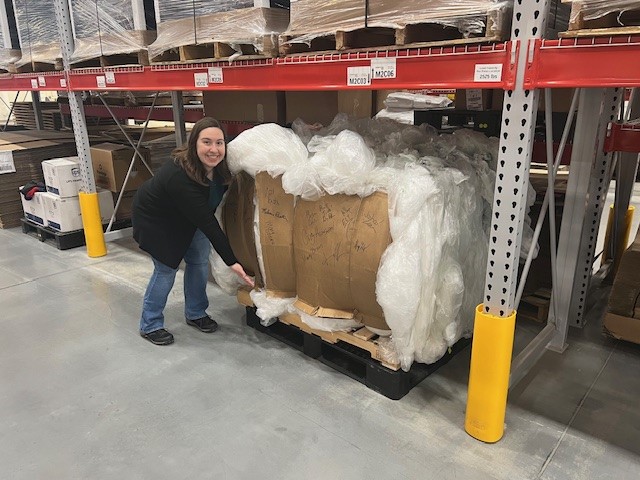
The baler was installed in Kepler Center in February 2024. Several employees were trained to use it, and they quickly started loading plastic collected from ten different locations at Promega Madison. The first bale was ejected on February 16 and a second bale followed soon after in March. The team expects to fill the first trailer for pickup within a year – around 35,000 pounds in twelve months.
“It’s so satisfying to see it in action,” Katelyn says. “It feels like it took a long time, but it feels good to get a project like this to completion.”
“As a science company, there’s no doubt this is the right thing to do,” Melanie adds. “We’re doing something impactful for the environment and for our community. We’re building relationships that will help us reach our bigger sustainability goals.”
The team says that in the coming months they hope to expand and capture more of the plastic film consumed at Promega, including from office areas and kitchens. They’re also turning their attention to other potentially recyclable materials at Promega. For example, in April 2024, battery recycling was expanded to include more battery types, and employees are welcome to bring used batteries from home.
“We have to keep the momentum,” Melanie says. “If we leverage our success, focus on getting people educated and excited, we can continue making a real, tangible impact.”
Learn more about Promega sustainability programs in our Corporate Responsibility Report.
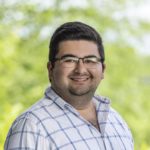
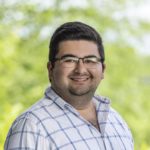