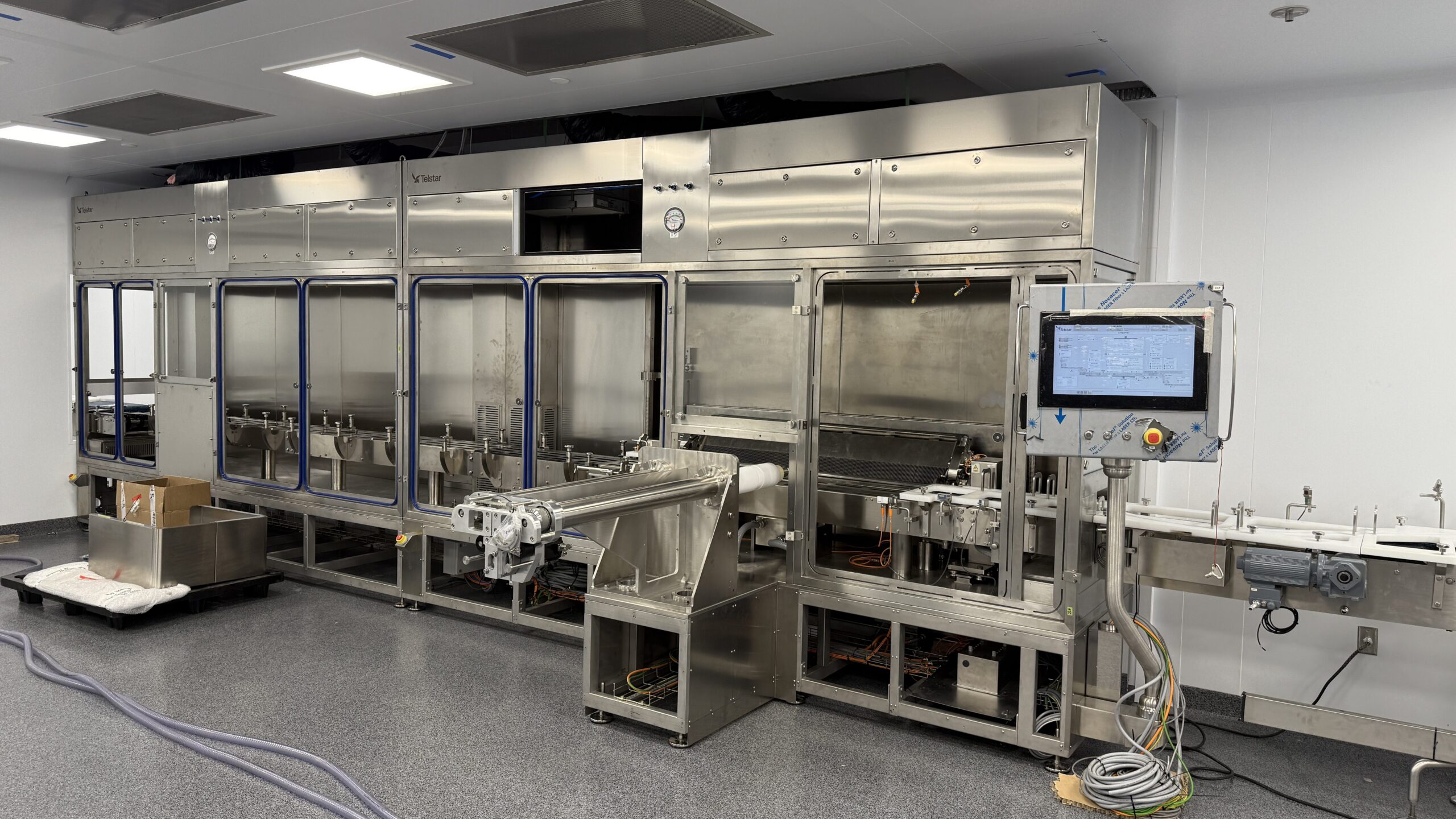
On March 12, 2025, a 46,000-pound stainless-steel chamber made a five-hour journey through Feynman Center to its final resting place in the brand-new Fill-Lyophilize-Finish suite. This massive piece of equipment will more than double the lyophilization capacity at Promega Madison, safeguarding the continuity of production and opening new frontiers in product formulation.
Lyophilization provides scientists with increased stability, enhanced flexibility and protection against error. Promega has been lyophilizing reagents in-house since the mid-1990s, and demand has steadily grown over time. The recent expansion reflects the company’s commitment to anticipating scientists’ future needs and planning for the long term.
Why is Lyophilization Important?
Lyophilization, also known as freeze-drying, provides a variety of benefits in the lab. For example, lyophilized reagents can typically be stored at higher temperatures, and they offer longer stability.
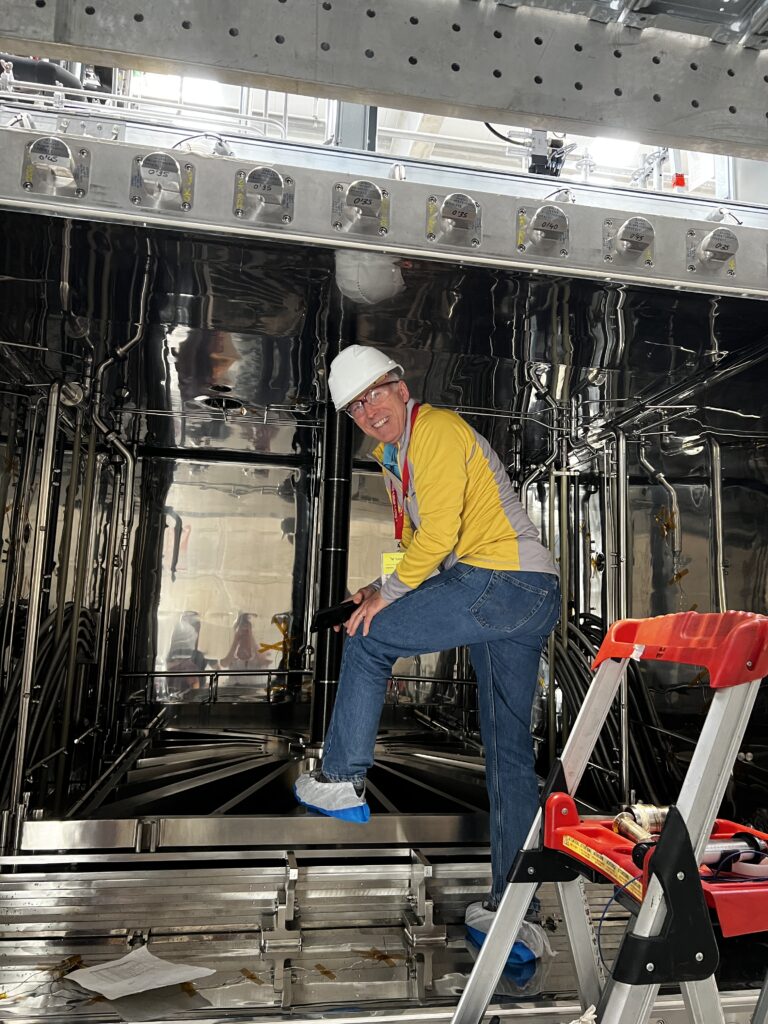
“Lyophilized product also gives you added flexibility in how you tailor your reagents to your specific need,” says Stuart Forsyth, Sr Process Validation Engineer at Promega. “Whether you’re reconstituting with a buffer, water or even a sample, you’re able to alter the assay’s concentration and formulation in ways that are impossible with liquid formulations.”
Many of the most popular Promega products include lyophilized components, including the CellTiter-Glo® Luminescent Cell Viability Assay and ONE-Glo™ Luciferase Assay System.
Promega also offers lyophilization for customers working with Promega to manufacture custom products. The flexibility helps many labs, especially diagnostics, ensure that the final reagent maximizes efficiency and ease of use for point-of-care applications.
“Especially if you’re lyophilizing the whole assay in one, you’re removing a lot of potential for mistakes by the user that would result in product failure,” says Terri McDonnell, Director of Global Custom & OEM Commercial Development. “Lyophilization capabilities are powerful tools to have in your toolbox as you try to formulate a reagent for minimal risk of misuse or mistakes.”
Expanding Lyophilization at Promega Madison
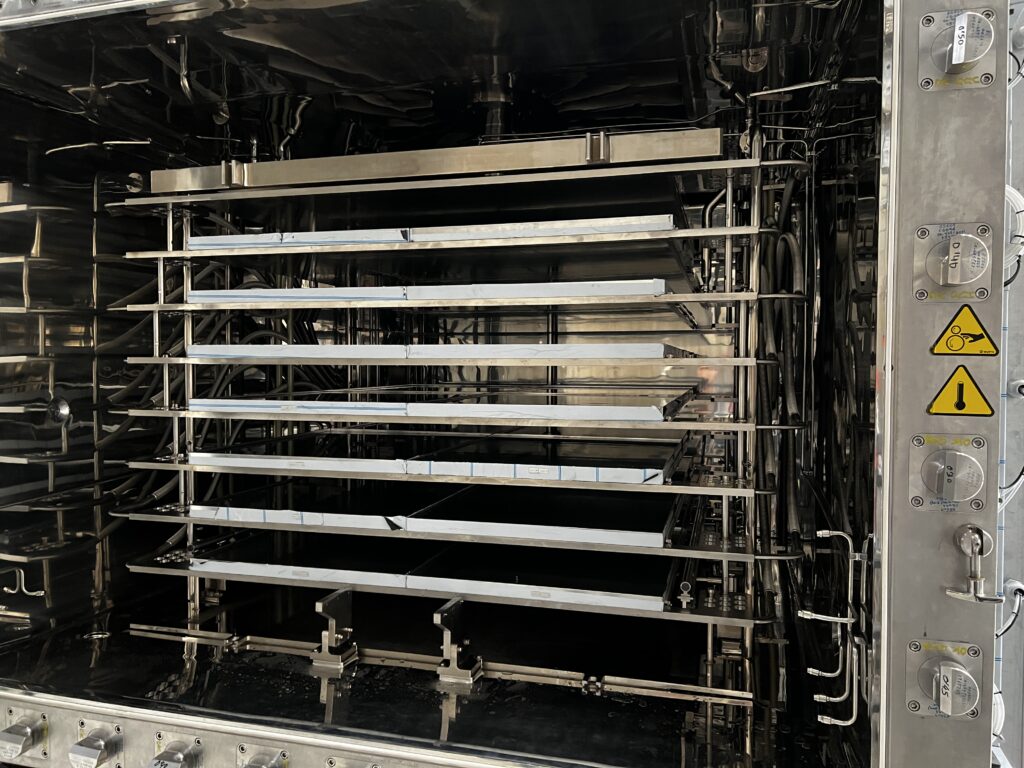
Promega Operations closely monitors the throughput capacity of all critical processes. For years, the team has projected that manufacturing would outgrow the existing lyophilization capacity sometime in the mid-2020s. The project to build out the empty suite in Feynman Manufacturing Center began in 2021, and it will start producing products for sale in early 2026.
The new lyophilizer nearly doubles the throughput capacity of Promega Madison. It will primarily be used with 10ml vials and 100ml bottles, but the line can also handle 2ml and 3ml vials and large LyoGuard trays for bulk powder production. At this point, the team plans to primarily use the Feynman suite for high-demand catalog products like CellTiter-Glo, creating flexibility to use the older lines for custom products and other smaller demands.
Continuity, Collaboration and Creativity
The new lyophilization suite will have several significant impacts for scientists using Promega reagents.
First, the new lyophilization line creates additional redundancy to ensure that key products are continuously available. The huge increase in capacity means that if one lyophilizer is down for maintenance, the others can handle picking up the slack. The new suite also features the current state-of-the-art automation technology, minimizing any risks for contamination or human error that would disrupt high-quality production.
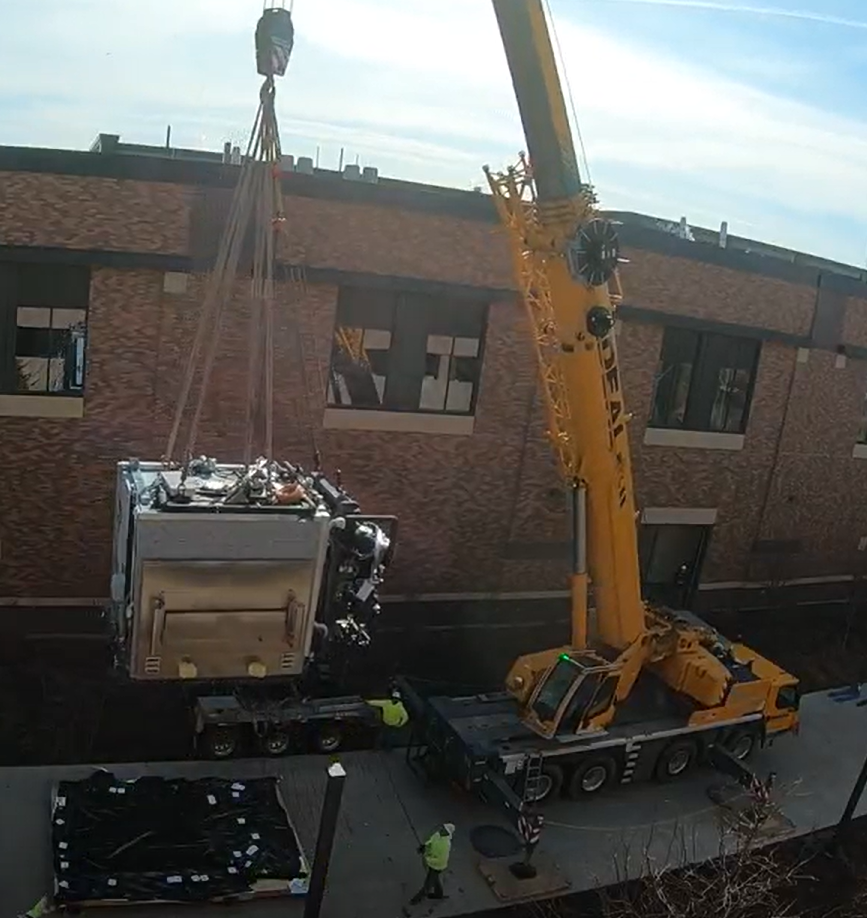
For customers working with Promega on custom orders, the new lyophilizer gives Promega more flexibility to collaborate with customers on finding the right formulation for their needs, all within the established quality system.
“We partner with a wide range of customers seeking to adapt or customize our technologies for specific applications,” says Terri McDonnell. “As the primary manufacturer of most of our products, and with the addition of new lyophilization capabilities, we can offer expanded scale and format options. Because these activities are performed in-house, we maintain greater control over quality and supply chain logistics, helping to ensure the consistent and reliable delivery of products.”
Finally, the additional capacity means that high-volume products can be manufactured less frequently by scaling up batch sizes. This frees up human resources to explore process improvements and dedicate more time to work outside of the production workflow. Kris Pearson, Director of Manufacturing Sciences and Custom operations, says the smaller equipment can serve as a sandbox where teams can test creative ideas.
“We’ll have more opportunity to work with R&D on new product development, and to dive deep into new cycles and what that can mean for our custom capabilities,” she says. “We can play around with new formats and processes to find new ways of offering a great product for every custom customer.”
Long-Term Planning and Strategy
As a private company, Promega isn’t beholden to short-term gains. Leadership prioritizes decisions that support future needs, while building in room to adapt to changes in the scientific landscape.
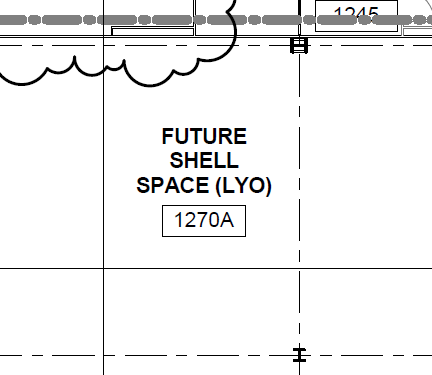
“When we started designing Feynman Manufacturing Center, we said we wanted 30% of the square footage to be frontier space,” says Jen Romanin VP of Global Support and IVD Operations, and key member of the Global Planning Team. “This space would give us future flexibility in where new features would be installed.”
Sometimes needs are forecasted far in advance – for example, the architectural drawings of Feynman Manufacturing Center dated February 2012 show the new suite was already earmarked for Lyophilization almost a decade before the construction project began. Other spaces are left intentionally unlabeled as a nod to the unknown needs that will emerge over time. Whatever arises, the flexibility and foresight built into Promega facilities will position the team to respond quickly – and build a high-quality solution – without having to break new ground.
“I think this says two things about us,” says Chuck York, Vice President of Operations at Promega. “First, it says we’re pretty confident we’re going to be here for a long time. Secondly, it says that no matter what happens between now and then, we want to make sure we’re prepared.”
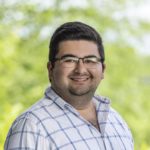
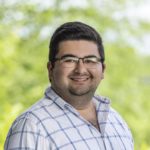